No two journeys along the same path are alike – each is paved with sets of unique experiences that shape the direction of the trek. This sentiment is especially true for 4 engineers from across different disciplines at Milwaukee Tool. These engineers chose to share their journeys with us so far – the challenges they’ve faced and the opportunities they’ve gotten to experience along the way.
Read their stories below or click one of their names to skip to your area of interest.
- Cyndi Petterson, Manager of Firmware Engineering
- Hannah Schultz, Packaging Engineer II
- Cameron Cashman, Manager of Automation Engineering
- Heungkuk Choi, Electrical Engineer
Cyndi Petterson
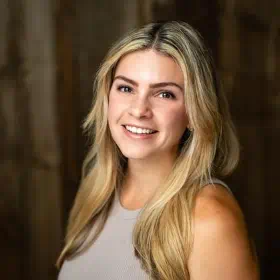
Joined Milwaukee® Team: 2020
Location: Brookfield, Wis.
Responsibility: Leads Firmware Support for power tools, overseeing a team that completes firmware anomaly fixes, new feature development and other overall support.
Alma Mater: Milwaukee School of Engineering (Bachelor of Science, Electrical and Electronics Engineering)
Q: Tell me a little bit about your background.
CP: When I graduated from MSOE, I worked for more than 8 years at another large company in southeastern Wisconsin that delivers industrial automation solutions. I started out doing electrical engineering testing, but then got the chance to move into a firmware test role where I got to learn what firmware is and how to test it. Eventually I was doing full firmware automated testing for PLCs.
Q: Why leave that company and join Milwaukee Tool?
CP: Ultimately, coming out of the pandemic, I was ready to change gears. That’s when I found my role at Milwaukee Tool – they had an open test position for a new test team (what’s now known as our HIL test team) to do automated hardware in the loop testing of firmware.
I knew a lot about Milwaukee Tool from MSOE – it’s a hot place to work and I have fellow graduate friends here. I was able to find a role and make of it exactly what I wanted… this is my dream job.
Q: You mentioned this was a ‘new’ team. What was that like?
CP: Really exciting. I got to help establish a brand-new team here – how we’d function, how we’d interact, how we’d work. I was the second person brought in on this HIL team, and it's been incredible to see the growth!
Because of what I was able to accomplish in a short time here, I moved into more of a technical lead role as we grew. But soon leadership wanted to make a new sub-org that could act as support for this new team and, before I knew it, I was in the running to lead it!
The growth of this company is incredible and it’s creating tons of opportunities. Meanwhile, leadership is investing to support these opportunities. It’s invigorating.
Q: What’s been your favorite project to work on?
CP: I have a group of highly skilled firmware engineers that report to me. We get to work with every new power tool development team at this company. Specifically, in my position, I meet with leadership regularly to understand their feedback on the work my team is providing and anything else we can be doing to assist in developing these new products.
The project that has stuck out with me the most has been a tool under the Drilling and Fastening category. My team helped add 5 features to a product all at once – these features had to be integrated quickly and effectively. Ultimately, these features helped the tool reach an optimal noise level so it can be used in environments with regulatory noise constraints. I was proud that my team was able to tackle adding these features quickly and productively. Not to mention, these features give us a great competitive edge in the market!
At any one time our team can be working on any number of things – we’re empowered to prioritize, delegate, escalate. And, of course, sometimes we must hustle to address bugs in a short window of time, but that’s one of the parts of Milwaukee Tool’s “agile” culture that I love – we must be able to drop and shuffle constantly. I find that fun.
Q: Is the speed at which we work pretty different from where you were before?
CP: Absolutely. At my previous company, a typical project could take 4 years. Here, it’s often 18 months! It’s such a scaled down amount of time to develop, test, and ship these products out all without sacrificing quality. It’s part of what has made this company so successful, but I also recognize it can be a stressor sometimes so I really make it a point to try and support my team through this speed as much as I can and make sure they have the resources they need.
Q: What has been the most challenging about developing a team where you aren’t doing the technical work yourself, but you’re overseeing it all?
CP: Managing expectations. Once people know that you’re around and here to help, they’ll come to you with anything. I will fight for my team and their bandwidth. So, a lot of what I do is helping our internal customers understand what’s possible and when.
Q: You’ve said this is your dream job. What else makes you excited about being here?
CP: My voice is so much louder here. I feel heard, every day. We do regular skip-levels with management (even as far up as our VPs), and I know my feedback is being listened to and acted on. That’s something that blows me away about working at Milwaukee Tool.
Hannah Schultz
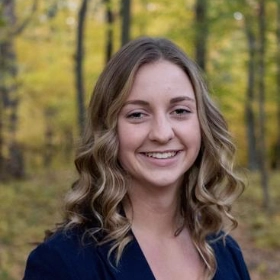
Joined Milwaukee® Team: 2020
Location: Milwaukee, Wis.
Responsibility: Enhances and optimizes packaging design, testing, and project management.
Alma Mater: Michigan State University (Bachelor of Science, Packaging Science)
Q: Tell me a little bit about your background.
HS: I’ve always had an interest in STEM, and a creative side. When I was in high school, my dad recognized this and introduced me to a packaging engineer at his work whom I ended up job shadowing. I was really impressed how they could take a 2D design and be able to send it to a prototype table, cut it out, and make a sample in less than 5 minutes. That really stuck with me, and I ended up going to Michigan State which has the largest packaging program in the country.
Q: What eventually drew you to Milwaukee Tool?
HS: I didn’t know much about this company when I first started looking for a job – especially when it came to packaging engineering. What ultimately struck me was the recruiters I met at a job fair on my campus. They were young, super energetic, and genuinely cared about sharing their experiences with me. After hearing more about the growth and the opportunities I’d be exposed to at Milwaukee®, I knew it was the atmosphere I wanted coming out of college – and the passion of the people here was attractive.
Q: As a packaging engineer, what do you do?
HS: I design best-in-class packaging solutions that fulfill cost, performance, sustainability, and schedule targets for power tool products. At any one time I could be working on 10-20 different projects. As a packaging engineer I also get the unique opportunity to work cross-functionality with numerous different teams across the business including Marketing, Sourcing/Procurement, Operations, Distribution, Mechanical & Reliability Engineering, and our other packaging teams around the globe!
Q: Do you have a favorite project you’ve worked on?
HS: I have 2 favorite projects in my time here…
- When I first started working here, I immediately got to work on a hardhat/headlight promotional kit for one of our largest distributors. I essentially had to take 2 existing products and put them together into a special kit configuration. This project was a great learning experience because the cross functional team included some members that typically work on hand tools projects and others that work on power tools. I was able to quickly understand key differences between the functions of the business units. It was challenging because we not only had to meet merchandising requirements, but we also had to make the packaging design interactive so customers could feel the hard hat and turn the headlight on while shopping. We ended up creating a solution with a box and clamshell inside that was ultimately so successful that we’re now using this concept for other products.
- This one was a MUCH larger tool – the MX FUEL™ Screed. Because of how large equipment like this is sold, we were less concerned with how the packaging helped merchandise it and more concerned with the packaging protecting it. Screed bars are up to 16’ in length and need to be straight when they get to the user. My focus was on testing and designing packaging that could go through distribution and arrive to the customer in perfect condition. I spent a lot of time making different pallet patterns, truck loads, working with suppliers and distributors – we had to make sure they could handle different configurations without extravagant shipping costs. With a lot of support from our distribution center we have developed a unique way to successfully deliver these to customers.
Q: So, you’ve been here a couple years now – what keeps you at Milwaukee Tool?
HS: A couple things:
- The atmosphere. This company continues to grow so fast, and there’s lots of positivity around that. One of the things that attracted me to Milwaukee® in the first place – the People – is a big reason why I stay. I’ve created a great network here, especially in our Engineering Development Program.
- The projects. A lot of my peers from college work for food companies where there’s a lot more competitors to reference from a packaging perspective. Here, we’re working on a lot of unique and new products. You get a large range of experiences here which has been a great learning experience.
- The challenge. I continue to be challenged every day. I feel valued as an employee and my managers keep finding new ways to challenge me in my role and find new opportunities to grow me.
Cameron Cashman
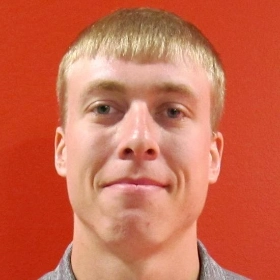
Joined Milwaukee® Team: 2018
Location: Menomonee Falls, Wis.
Responsibility: Designs and implements new and existing automated testing equipment.
Alma Mater: University of Wisconsin - Madison (Bachelor of Science, Mechanical Engineering)
Q: Tell me a little bit about your background.
CC: Throughout my time at UW-Madison, I had an internship at a company that develops gearmotors and motor solutions. I started out in the manufacturing setting and then got more active in automated solutions for automated testing. After school, I knew I wanted to get a job in automation because that’s where I knew my skills were strongest. Through my intern experience I realized that I was not just a mechanical engineer – I aspired to know the electrical side and the programming side. So, automation just made sense.
Q: What drew you to Milwaukee Tool?
CC: I’ve grown up using Milwaukee® tools so I knew the quality of the product, but I had no clue about the company itself. Ultimately, during a job fair, I found out that Milwaukee Tool has a wonderful in-house development lab for test solutions. I applied and got to take on an exploratory or investigative engineering role at Milwaukee® on the test side. It was an opportunity I couldn’t pass up.
It was a little intimidating, though. I was walking into this big company and the level of innovation surprised me.
Q: Have you had a favorite project that you’ve worked on?
CC: The best part of working in an Engineering Support Group is that I’ve gotten to work on a large variety of projects in my time here, but one of my favorites was a test system called “Auto-Indexing Vacuum Plenum.” It was one of my favorites because it was an endeavor where, as the sole Automation Engineer, I was able to tap into multiple engineering disciplines and apply them to the Mechanical Design, Electrical Design, and Software Programming. It was also my second year here so it allowed me to showcase to the team what I could bring – and I was empowered to own it! I had mentors, and a review team… but I got to make the decisions and react the way I needed to. The result is something we still use today.
Q: What was most challenging about this?
CC: The entire project was born from improvements we needed to make to the existing test system, which had been manually operated and collected insufficient data for energy correction of air flow. Therefore, it required an operator to interact with the test and later perform post processing on the data. In the end, collecting test data was time intensive, incomplete, and prone to errors. The 2 biggest challenges when designing this system were:
- Designing a compact mechanism that would not only rotate or index to a new orifice size but would also seal against an intake gasket.
- Ensuring that uncertainty calculations across all hardware or signal interactions were accurate enough to pass the tight calibration specs to comply with the testing standard.
Q: What was it like to solve these problems in the end?
CC: In the Engineering Support Group, we don’t get the pleasure of seeing our products in the hands of our end users, but we do get the pleasure of witnessing our own engineers making discoveries that would not be possible without custom test systems – and that’s a pretty sweet feeling.
Q: What keeps you at Milwaukee Tool?
CC: The energy and investment into in-house, custom solutions. I have never seen a company so invested in the premise of “We’ll just do it ourselves.” There’s so much opportunity here if you’re inquisitive enough. There’s no red tape – if you make a good case, leadership invests in your idea. You’re expected to build the plan, take calculated risks, and prove out solutions. That level of investment into employee growth is remarkable.
Within 5 years I got the opportunity to become a manager. The training and development I’ve received here has accelerated my career beyond what I could have imagined.
Heungkuk Choi
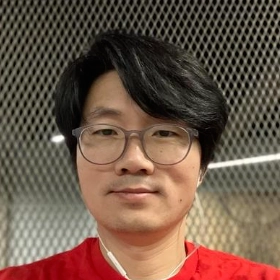
Joined Milwaukee® Team: 2022
Location: Chicago, Ill.
Responsibility: Creates developmental testing procedures in collaboration with New Product Engineers.
Alma Mater: Brigham Young University (Bachelor of Science, Electrical Engineering)
Q: Tell me a little bit about your background.
HC: I went to many different schools prior to getting into Electrical Engineering. I studied drafting, academy design, architecture, biology, and mechanical engineering. My interests changed a lot, but I worked throughout all my school years – from designing and manufacturing surveillance cameras for nuclear reactors to aerospace and cellular networks. Around the time that I really got interested in Electrical Engineering, I moved from South Korea to San Diego and pursued a degree with Brigham Young University in Idaho.
Q: What drew you to Electrical Engineering in the end?
HC: After seeing a Ted Talk on the topic, I got really interested in quantum computing. I ended up taking a class about signal and power integrity – all about how to control the signal and power on a circuit board. That really got me into electrical engineering and was the class I enjoyed the most.
Q: How did you end up at Milwaukee Tool?
HC: I’ve owned Milwaukee® tools, but to be honest I hesitated to apply here at first because of the Wisconsin location. But out of sheer curiosity I decided to apply and see what happened because I really liked the engineering design of the tools.
At the time, several companies wanted me but Milwaukee® ultimately stood out because of the experience I had during the interview process. I really enjoyed talking to everyone – especially the managers. I even got to speak with the manager I’d be working with; we had a similar background and got me intrigued in the types of projects I’d be working on. An added bonus was that I’d get to work in the new Chicago office.
Q: In your short time here, have you had any favorite projects?
HC: Yes. For background – I mostly assist our ongoing New Product Development (NPD) on developmental testing procedures to ensure quality of product. I design and run the tests, upload the test data, and discuss findings with the project teams.
I’ve been working on testing for a fastening tool and it’s my favorite because it’s been a big learning experience for me. When I first started working on it, I made a lot of mistakes, but those mistakes really pushed me and taught me how to run the testing properly and how to protect prototype PCBs. I’m also learning how to modify the firmware. I haven’t been here very long and I’m already getting to learn how to use and revise firmware, and how seed programming works with the tool. I’m also learning about the different components – micro control units, gate drivers, MOSFETS, how the capacitors affect signal quality and integrity. All of these things fascinate me – there’s so much that goes into running these tools.
Q: You mentioned you were originally hesitant to apply at Milwaukee Tool. Do you feel you made the right decision to join the team?
HC: Yes. The biggest thing that convinced me I made the right choice was seeing how employees are treated here – especially when it comes to learning and access to teaching and coaching. In all the other companies that I used to work for, there was far less open communication. You couldn’t go to another department and ask questions if you were curious about something. Here, if you’re interested and want to learn, you know you can reach out to anyone and they’re willing to teach you. That really stands out from any other company.
Find Your Place Among Our Innovators
If you’re interested in Engineering jobs at Milwaukee Tool, you can visit our Engineering career site at the button below to learn more and find open roles.